Tracking
Tracking lucas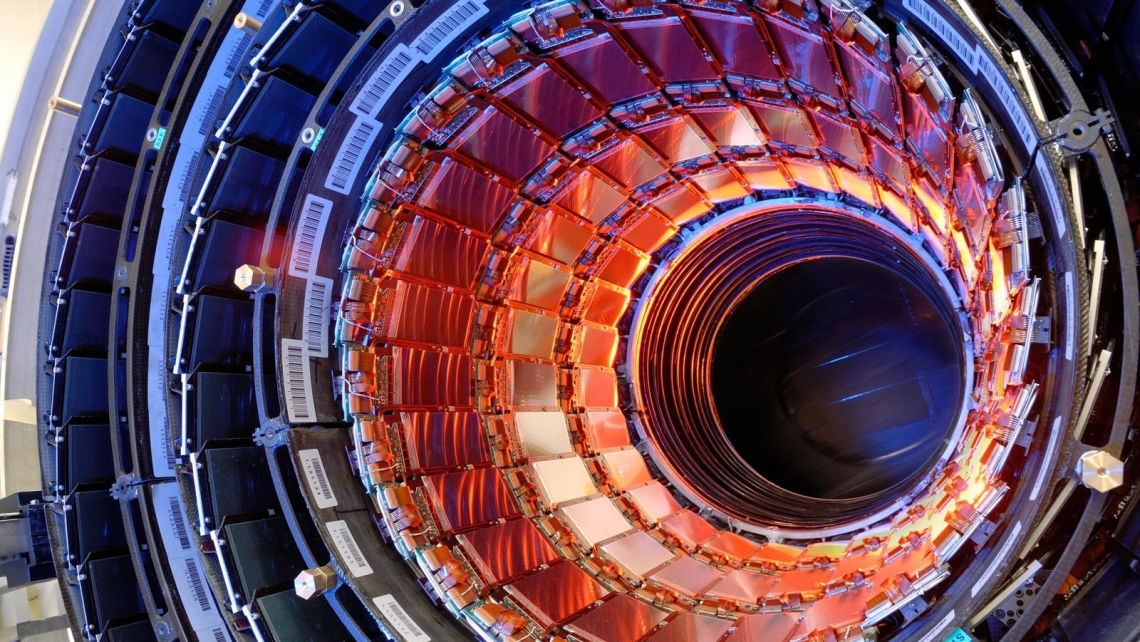
The measurement of the momentum of particles is crucial in helping us to build up a picture of what happens at the heart of the collision. One method to calculate the momentum of a particle is to track its path through a magnetic field; the more curved the path, the less momentum the particle had. The CMS tracker records the paths taken by charged particles by measuring their positions at a number of points.
The tracker can reconstruct the paths of high-energy muons, electrons and hadrons (particles made up of quarks) as well as see tracks coming from the decay of very short-lived particles such as beauty or “b quarks” that are for example being used to study the differences between matter and antimatter.
The tracker needs to record particle paths accurately yet be lightweight so as to disturb the particle as little as possible. It does this by taking position measurements so accurate that tracks can be reliably reconstructed using just a few measurement points. Each measurement is accurate to 10 µm, a fraction of the width of a human hair. It is also the innermost part of the CMS detector and so receives the highest volume of particles: the construction materials were therefore carefully chosen to resist radiation.
The final design consists of a tracker made entirely of silicon detection elements: the pixels, at the very core of the detector and dealing with the highest intensity of particles, and the silicon microstrip detectors that surround it. As particles travel through the tracker the pixels and microstrips produce tiny electric signals that are amplified and detected. The signals are stored in chips’ memory for several microseconds and then processed before being sent to a laser to be converted into infrared pulses. These are then transmitted over a 100m fibre optic cable for analysis in a radiation-free environment. The tracker uses 40,000 such fibre optic links providing a low power, lightweight way of transporting the signal. Much of the technology behind the tracker electronics came from innovation in collaboration with industry.
The tracker employs sensors covering an area the size of a tennis court, with 135 million separate electronic readout channels: in the pixel detector there are some 6600 connections per square centimetre. Silicon sensors are highly suited to receive many particles in a small space due to their fast response and good spatial resolution.
The CMS strip tracker was installed in CMS in late 2007 and has been in continuous operation since 2008. The original CMS pixel detector was operated during the years 2009 – 2016 and was replaced by the CMS Phase-1 pixel detector in an extended year-end stop 2016/2017.
Visit the link for Pixel Tracker updates: https://cms.cern/tags/tracker
More details about the CMS Tracker can be found in the following selection of documents:
The CMS experiment at the CERN LHC (paper written in ~2008 describing the original CMS experiment as build for LHC Run 1)
The CMS Phase-1 Pixel Detector Upgrade (paper from 2020 describing the Phase-1 pixel detector)
The very original description of the CMS tracking detectors can be found in the Technical Design Report (TDR) from 1998 and 2000, respectively
CMS: The Tracker Project Technical Design Report
The CMS tracker : addendum to the Technical Design Report
While many design aspects have evolved from the original concept, they still provide interesting insights about the challenges for the detectors and how they were thought to be overcome. A few more words on this are in the following paragraph.
Some design history ...
In the very first design sketch of CMS, the tracker section was left blank because it was thought that with the intensity of particles experienced in the LHC it would be impossible to make a tracker that could withstand it. In particular, making readout electronics that could work in this radiation would be a challenge. Hints that the US military, needing such electronics for space travel and nuclear warheads, might have solved some of the potential problems encouraged the team to explore this field.
However, the technology actually came from a most unexpected source; as the military market shrank at the end of the cold war and commercial electronics began to excel, the team took a gamble on a very fine feature manufacturing process, produced for a commercial market, which was not formally in the realm of “radiation hard electronics”. With some modifications, a few simple design tricks and selection of the right technology, it could be as radiation hard as needed. And it was a remarkable success. Eighteen months later the teams had rebuilt the old chips. They had low power consumption, low noise, and high overall performance and on top of this could be easily produced on a large scale, were relatively cheap and thoroughly tested. It was a big breakthrough. The same technology was then also used for the ECAL as well as CMS and ATLAS pixels.
Silicon Pixels
Silicon Pixels lucas
The pixel detector, though only about the size of a small suitcase, contains 124 million pixels, allowing it to track the paths of particles emerging from the collision with extreme accuracy. It is also the closest detector to the beam pipe, with cylindrical layers roughly at 3cm, 7cm, 11cm and 16cm and disks at either end, and so will be vital in reconstructing the tracks of very short-lived particles.
Each of the four layers is composed of individual silicon modules, splitted into little silicon sensors, like tiny kitchen tiles: the pixels. Each of these silicon pixels is 100µm by 150µm, about two hairs widths. When a charged particle passes through a pixel, it gives enough energy to eject the electrons from silicon atoms. A voltage applied to the sensor allows collecting these charges as a small electric signal, which is amplified by an electronic readout chip (for a total of 16 chips per module).
CMS silicon pixel detector
Knowing which pixels have been touched allows us to deduce the particle's trajectory. And because the detector is made of 2D tiles and has four layers, we can create a three-dimensional picture.
However, being so close to the collision means that the number of particles passing through is huge: the rate of particles received at 3cm from the beamline is around 600 million particles per square centimetre per second! The pixel detector is able to disentangle and reconstruct all the tracks particles leave behind, and withstand such a pummeling over the duration of the experiment.
Because there are 124 million pixels, the power for each must be kept to a minimum. Even with only around 50 microwatts per pixel, the total power output is 7.5kW- around the same as the energy produced by two electric ovens. So as not to overheat the detector, the pixels are mounted on cooling tubes and kept at -20°C degrees. Operating at this temperature also helps to reduce the effects of the damage to the silicon modules inflicted by the continuous stream of particles.
Visit the link for Pixel Tracker updates
Silicon Strips
Silicon Strips lucas
After the pixels and on their way out of the tracker, particles pass through ten layers of silicon strip detectors, reaching out to a radius of 130 centimetres.
The silicon strip detector consists of four inner barrel (TIB) layers assembled in shells with two inner endcaps (TID), each composed of three small discs. The outer barrel (TOB) – surrounding both the TIB and the TID – consists of six concentric layers. Finally two endcaps (TEC) close off the tracker on either end. Each has silicon modules optimised differently for its place within the detector.
This part of the tracker contains 15,200 highly sensitive modules with a total of about 10 million detector strips read by 72,000 microelectronic chips. Each module consists of three elements: one or two silicon sensors, its mechanical support structure and readout electronics.
The silicon detectors work in much the same way as the pixels: as a charged particle crosses the material it knocks electrons from atoms giving a very small pulse of current lasting a few nanoseconds. This small amount of charge is then amplified by Analogue Pipeline Voltage (APV25) chips, giving us “hits” when a particle passes, allowing us to reconstruct its path. Four or six such chips are housed within a “hybrid”, which also contains electronics to monitor key sensor information, such as temperature, and provide timing information in order to match “hits” with collisions.
Due to the nature of their job, the tracker and its electronics are pummelled by radiation but they are designed to withstand it. To minimise disorder in the silicon this part of the detector is kept at -20oC, to “freeze” any damage and prevent it from perpetuating.
CMS Tracker layers shown in the plane perpendicular to the beam.