Civil Engineering
Civil Engineering lucasThe CMS cavern, at Point 5 of the LHC near Cessy, was excavated from scratch in an old LEP (a previous CERN accelerator, the Large Electron Positron Collider) access point. The work, which took six and a half years, finishing in February 2005, consisted of creating two caverns 100m underground, including the 53-metre long, 27-metre wide and 24-metre high experiment cavern, as well as two new shafts.
CMS is like a cylindrical onion built around the beam pipe, but cut up into 15 slices. The experiment employed a unique method of construction: assembling and testing each of the slices of detector on the surface before lowering them underground, rather than building the components within the cavern itself. This meant having to transport and lower huge but delicate pieces of detector, weighing as much as 2000 tonnes, down a 100-metre shaft but also gave a number of advantages. Not only did it enable civil engineering work on the cavern to go on in parallel with detector construction, but also the ‘slicing’ means that each piece remains accessible for ease of maintenance within the cavern.
Because of this method, CMS was in a unique position to be able to excavate where geology was difficult, without any delays hampering the progress of the detector itself. And at Cessy the ground is indeed difficult: 75 metres of “moraine”, a glacial mixture of sand and gravel containing two water tables, followed by “molasse” rock, a form of soft sandstone. To excavate through this loose earth and soft rock and to build a cavern without it collapsing was an enormous challenge. To find out how they did it, click here
Facts about CMS civil engineering…
- Whilst excavating trial pits around the site engineers found a Roman villa complete ancient with pots, tiles and coins
- Soil removed during excavation was made into an artificial hill on the site
- The company that performed the heavy lowering also constructed the walkway between the Kuala Lumpur twin towers and built a stadium in Durban, South Africa, for the 2010 World Cup
- The heaviest piece lowered weighed 2000 tonnes and took 12 hours to travel the 100m underground
CMS assembly
CMS assembly lucas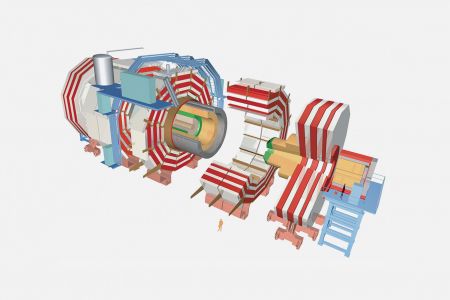
The decision to employ a method that involves hoisting thousands of tonnes of expensive machinery, the result of endless hours of work, down a 100 metre gaping hole was never going to be taken lightly. But CMS’s unique method of slicing up the detector and lowering each piece into the cavern ready-made, has been nothing short of a success.
“It’s a huge amount of responsibility; you have all the physicists waiting for an element to arrive, and if you make a serious mistake, it could be the end of CMS,” says Hubert Gerwig, whose task it was to ensure each sub-detector’s safe arrival.
But lowering CMS by means of heavy lifting was a decision taken at the very beginning, some 16 years ago, inspired by experiences with LEP. “The concept of building large objects on the surface and transferring them completed to the underground area was the clear way to go,” says Alain Hervé, CMS’s original technical coordinator. Though not in LEP’s initial plans, success in lowering two pieces into position in L3, weighing 300 and 350 tonnes, suggested the method could work.
Being able to work in parallel on the civil engineering and the detectors was clearly a huge advantage, and the ‘slicing’ also meant that, through complicated loops of cable chains, water, gas and cooling leads, each piece remained accessible within the cavern, a contrast with experiments built in a ‘Russian dolls’ style, from the inside, out.
But the implications of using this method needed careful consideration too: “As soon as I saw the sketch I had a clear vision of how such an experiment had to be organized,” says Alain. “We were already two years inside LEP running, and lessons from the construction and the first shut-downs were clear to me. The way the experiment had to be sectioned and installed was the first priority, not developing the design,” says Alain.
And so the experimental area, pits and surface hall all had to be designed around the lowering method. Foundations for the gantry and a massive strong plug to hold the pieces over the shaft before the cranes took the strain were incorporated. Anchor points for lifting were integrated in the design of the yoke as well as HCAL (Hadron Calorimeter) and HF (Forward Calorimeter) platforms and cradles.
The first lowering took place in November 2006, and the last on 22 January 2008. “Everything has been calculated and calculated again, but that’s still not the real thing,” says Hubert. “In the end we were successful and nothing was damaged. So there is a sense of relief; it’s a bit like an exam, you feel better once it is over and you can celebrate!”
Heavy lowering
Heavy lowering lucas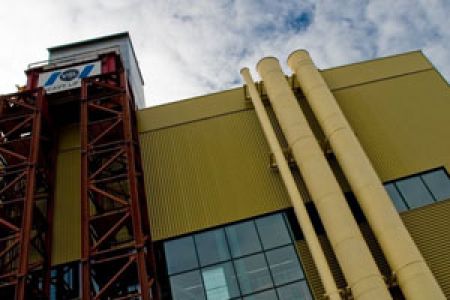
Trials and Tribulations of Heavy Lowering
Ten companies internationally were capable of taking on such a project as CMS, but VSL Heavy Lifting, a Swiss company, were the eventual winners of the 2 million CHF contract.
Though VSL were used to lifting such heavy loads as the 7500-tonne roof of the Airbus Assembly Hall, and the walkway between the Kuala Lumpur Twin Towers, CMS presented unique challenges. For a start, the equipment needed to lower, not lift, and a long way. Adding to this was the fact that the scientific cargo was far more delicate than its industrial counterparts.
The gantry support system was rented and made from existing towers, but the 3.4m high horizontal beam, that took the strain of the load, had to be custom made. Even such an enormous beam still bent 5cm under the weight of the heaviest element, the 2000 tonne central barrel ring known as YB0.
During each lowering, the element is supported at four points, but by many more cables as each bunch is made up of 55 individual 15.7mm diameter strands of cold-drawn steel, each with a capacity to hold 28.4 tonnes. Within each bundle, half of the strands are twisted one way and half the other to make overall turning force zero and preventing any turning of the load during the descent.
The lowering in fact happens in 200 small steps as the cables are fed through the hydraulic system half a metre at a time. This works on a grip and release basis, similar to your own hands lowering a bucket down a well, and at all times the load is safely supported by one or other of the clamping mechanisms. Once the cargo reaches the ground, it comes to a soft landing on hovercraft-like airpads that take the load off the cables and later on allow easy horizontal movement within the experiment hall.
Each lowering was a big event, requiring a week’s preparation to manoeuvre the plug, element and attachments in place, and each was a success. Though there were also, of course, a few challenges that arose along the way: YB0, for instance, the largest segment to enter the cavern, at one point cleared the sides of the shaft by just 10cm either side, and the team needed surveillance video cameras to carefully monitor its movements and ensure that the element passed the bottleneck safely.
The slight slope in the CMS cavern presented another issue. Whilst unnoticeable underfoot, the 1.23% gradient meant that when one side of any element touched down, the other still had 3cm to go. “Initially we tried to compensate for the slope, so that there was an even landing,” explains Hubert Gerwig, the engineer in charge of heavy lifting, “but soon we realised it wasn’t necessary because under the load, the metal strands actually elongate by 10cm, making them somewhat elastic.” The elasticity meant they could simply carry on lowering the piece until both ends were on the ground, also giving rise to the slight “bouncing” effect visible as each piece finally came to rest on the experiment hall floor.
That some of the elements couldn’t be supported on just four attachment points presented another issue and the endcap disks , for example, were instead carried down on a special crate. But being supported nine metres below their centre of gravity made them naturally unstable. The team solved this dilemma by using stabilisers at the top of the endcap such that if it tilted, it would simply lean against the lowering cables.
In the end each slice of CMS found its way to the experiment hall safely, thanks to the hard work and dedication of all involved, and the group and their equipment can now be disbanded. The VSL team will now take their gantries and hydraulic equipment to Durban in South Africa to build a stadium for the 2010 World Cup. Some parts, such as the cables that have carried down every piece of CMS, are now too fatigued to be used again. Finishing the lowering is a sad event for some, but the VSL mechanics like to travel the world and are eager to move on. “I think some of the workers get the opposite of home sickness,” says Hubert, “they cannot wait to get away again!” And we wish them good luck.
Massive underground excavation
Massive underground excavation lucasBetween 1998 and 2005 a total of almost 250,000 m3 of soil and rock was excavated from the CMS site at “Point 5” of the LHC, in Cessy. The contractors - Seli, an Italian company and Dragados, Spanish - had previously worked on the Madrid metro but here faced some unique surprises.
It started with an unexpected find: “We did trial pits around the site, because the archaeology of an area is always something we have to consider, and what we found was great – a Roman villa, complete with pots, tiles and coins,” explains John Osborne, project manager of CMS civil engineering. “And even better for us was that it wasn’t anywhere near any planned shafts or buildings.”
They were able to leave archaeologists to spend a year thoroughly investigating the site whilst the project got underway. But it wasn’t an easy task. “Funnily enough Point 5 was one of he worst places possible to build the cavern in terms of geology, though best from a physics point of view. And CMS was pretty much the only experiment that could cope with being built here,” remarks John.
The first challenge came in the form of underground water tables approximately ten to twenty metres below the surface. To dig down through them the team had to first freeze the ground around the shafts to act as a barrier to the water. By drilling holes around each shaft’s circumference and pumping down brine, cooled to -25oC, the water froze into a 3-metre wall of ice. But the water coming from Cessy was moving even faster than predicted, and combined with the channelling effect of water between the two shafts, pressure built up until it penetrated the walls.
Injecting the holes with an even colder substance: liquid nitrogen, at less than at -195oC, finally solved the problem. With its help engineers formed a wall of ice around the shafts that was solid-enough for teams to keep on digging.
However, the problems were not over yet. Once the shafts were dug out, work had to begin on the caverns, but because the ground materials were so soft, with no intervention any cavern excavated would collapse. “At Point 5 there is only 15 metres of solid rock. For the first 75 metres of digging down it’s just a type of glacial deposit called moraine - basically a mixture of sand and gravel,” explains John. “And the rock we did have was a kind of soft sandstone called Molasse. A large cavern built in this would just collapse.”
The solution was to build a large supporting structure underground that could hold up the caverns and withstand the mass of the soil above it. Engineers envisaged a concrete pillar as the divider between the two caverns that could do just this.
“Knowing we would have to build this structure anyway, we asked radiation teams how thick we’d need it to be to protect people from radiation in the cavern next-door to the experiment,” explains John. “They gave the figure at 7 metres. The width needed to ensure adequate support for the caverns was 7.2 metres, so this worked out very well, and in fact the second cavern can now be safely used when the machine is on.”
After these delays, engineers experimented with using explosives to clear away rock at a faster rate, but in the end it had little benefit for a big disruption. Instead the best trick seemed to be to excavate small sections at a time and immediately install “shotcrete”, a sprayed concrete that sets as soon as it hits the walls, and drilling steel anchors that reached 12 metres into surrounding rock: “If we didn’t do this, the whole thing would collapse whilst we were building it. We constantly monitored any movement with a host of instruments and adjusted the support as necessary.”
For the workers on the site, another exciting yet daunting nature of working on the excavation was descending into the CMS cavern in the lift. During the construction period, access underground was via a lift cage being lowered down the shaft on a system of ropes. “This was good as it meant you could always be lowered to exactly the right level, as opposed to fixed lifts,” explains John. “But being on a rope also meant that it had a tendency to sway as you went down. And 100 metres is a long way!”
As the environment 100 metres below the surface is also full of water, the final stages involved waterproofing, installing drainage systems and painting the cavern, as water could otherwise turn soft rock into mud. “Once everything was in place we could seal off the cavern with waterproofing and put in a permanent concrete wall up to 4 metres thick, reinforced with steel bars.”
Throughout the whole construction, consideration for the environment was at the forefront of people’s minds. In order to keep noise levels to a minimum, sound barriers were built all around the site. And instead of removing the many tonnes of earth and rock excavated from the site, causing noise and road disruption, it was deposited right by the buildings, covered with fresh soil and planted with vegetation, creating a now flourishing artificial hill.
Whilst this was going on, thanks to the “pre-packaged” design of CMS, split up into 15 slices, where each is assembled and as near to complete as possible on the surface, work on building the detector could carry on this whole time. And once the cavern was complete, in 2005, pieces of CMS could be lowered underground and installed.
But though the civil engineering stage of building CMS is long over, the underground nature of the experiment must always be taken into account. Though the detector weighs almost as much as the soil and rock it replaced, the caverns within the spongy earth are like bubbles in water, and they could potentially rise by as much as one millimetre (mm) per year. Geologists predict that CMS, along with the immediately surrounding sections of the LHC machine, will rise 15 mm over 10 years. This may seem small, but when you think that the detector’s tracker and muon systems, for instance, must align to within 0.15 mm, one hundredth of the distance, this small amount becomes significant. In fact the ability to adjust by this amount is built into the detector and movement will be monitored throughout the life of the experiment, so civil engineering continues to play a part in the running of CMS.