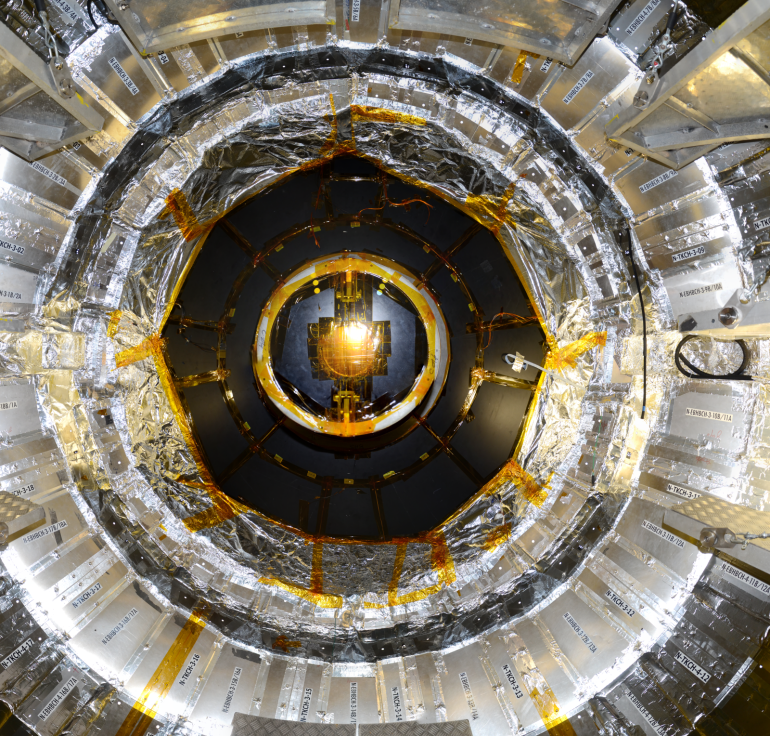
After two years of planning, one year of implementation, and two million CHF worth of investments, the Tracker project has achieved its most important goal to enable the “Tracker Going Cold”.
The Tracker was successfully (and safely!) operated “cold”, with the strips at T = −10 °C, for an extended period in late 2013. This run provided further directions for improvements, notably the repair of the vapor insulation of the (Tracker) cooling bundles. These had suffered damage in several places over the last few years and this resulted in the release of some water when warming up from sub-zero temperatures. In addition to the repair, a scheme of dry gas injection into the cooling bundles was designed and implemented, in order to fully address this earlier water release.
In late January, early February 2014 the Tracker passed the important ‘Master Cold Test’ milestone of CMS, and successfully operated the strip tracker at temperatures down to −20 °C with the pixel bundles even lower, at −25 °C. The detector performance, which was monitored continuously during this exercise, was found to be in line with expectation and requirements. Further important checks such as the thermal neutrality of the Tracker towards the ECAL crystals were also successful. This achievement represents the culmination of a long and painstaking series of steps and work over the past two years. A more detailed description is contained below.
The Tracker project has thus completed the bulk of its work for LS1, resulting in the ability to operate the detector cold with adequate safety margin. Small improvements are still being implemented and important discussions such as a possible backup solution for the dry gas are taking place.
Nowadays, the environmental conditions allow operation at −25 °C and the detector has been successfully operated at −20 °C. To minimize thermal stress, while still mitigating the effects of radiation, we are currently considering operating the strip tracker at −15 °C and the pixel at −20 °C for the upcoming LHC runs.
Bottom line: our Tracker is now ready to track particles until LS3!
Submitted by Nicola Bacchetta, Erik Butz, Francesco Palmonari, and Antti Onnela
Some details on what it took to make our Tracker cool…
There are several ingredients to this success: a) a largely refurbished cooling plant, b) an engineered vapor-sealing concept, c) heater elements outside the cold volumes (bulkhead and cooling ducts), d) high granularity and high-precision temperature and dew point sensors, and, most importantly, e) a very high flux of dry gas.
To augment the amount of dry gas supplied to the Tracker volume, a new dry gas plant, based on a membrane separation system, was installed by Technical Coordination. This new plant increases the total capacity of dry gas that can be delivered to the various parts of the system by a factor of almost eight from 55 to 400 m3/hr. In addition, new dry gas distribution pipes were installed. These allow for a fine-grained regulation of the dry gas flow predominantly to the most sensitive region, the Tracker bulkhead (see Image 1) and cooling bundles, even during beam operation.
To better monitor the humidity status as well as the temperature conditions during cold operation, several hundred (!) sensors were installed in the Tracker bulkhead, the service channels, and on the cooling bundles which house the cooling pipes circulating cold liquid to and from the detector. Two main types of radiation hard sensors are employed: fiber optic sensors (FOS) for humidity and temperature monitoring and industrial Vaisala dew point sensors placed in a dedicated analysis station away from the radiation zone which are sourced by sniffer pipes. In addition, non-radiation tolerant multi-sensors read out by Arduino microcontrollers have been installed which will serve as cross-check and help calibrating the radiation tolerant FOS.
The heater panels on the bulkhead panel have been reconnectorized for future ALARA-compatible access. In addition, all cooling bundles have been equipped on the outside with heater wires and temperature sensors to guarantee safe operation above the cavern dew point in the future; as a precaution if CMS would need to operate even below −20 °C before getting access to the outside of the vac-tank, which is actually not planned before LS3.
The humidity sealing and insulation of the Tracker and its service volumes have been largely improved. Several trials were performed during the early phases of LS1 leading to very encouraging results, while at the same time providing important hints that could only be obtained in-situ, for further improvements. The insulation concept tackles the problem of humid air ingress from all possible directions. Wherever possible, air paths towards the Tracker are blocked or narrowed as much as possible, newly designed pieces with additional insulation are placed to provided vapor barrier and insulation at the same time. For best possible results, vapor barriers are being installed even in service channels belonging to other subsystems of CMS.
Last but not least, the C6F14 cooling system was completely overhauled. As an example, new evaporators have been installed in the primary plant, as well as new heat exchangers in the UXC stations along with better control and monitoring capabilities. The stations have also been sealed much better with respect to humidity ingress, while the dry gas flow has been enhanced.
- Log in to post comments